產品目錄
蒸汽流量計
渦街流量計
孔板流量計
壓縮空氣流量計
氣體流量計
熱式氣體質量流量計
旋進旋渦流量計
金屬管浮子流量計
靶式流量計
電磁流量計
渦輪流量計
橢圓齒輪流量計
水流量計
液體流量計
超聲波流量計
磁翻板液位計
浮子液位計
浮球液位計
玻璃管液位計
雷達液位計
超聲波液位計
投入式液位計
壓力變送器
差壓變送器
液位變送器
溫度變送器
熱電偶
熱電阻
雙金屬溫度計
相關產品
聯(lián)系我們

聯(lián)系電話:15195518515
服務熱線:0517-86801009
公司傳真:0517-86801007
公司郵箱:1464856260@qq.com
公司地址:江蘇省金湖縣理士大道61號
關于一體化孔板流量計在機車鑄造技術中的改進措施及對策
摘要:針對日益發(fā)展的機車鑄造技術和成本控制,本文結合公司技改后采用 LF 爐精煉鋼包+熱裝一體化孔板流量計工藝,澆注前所產生的引流鋼過多,造成的鋼水利用率較低的頑固性難題,通過全過程因素分析,制定了工藝裝備、工藝參數,操作手段的改進以及建立電爐與澆注工序考聯(lián)動核競爭制度等方面入手,著手改進,取得了顯著成效。
引言 我公司自 2009 年技改后,電爐采用偏心爐+LF 爐雙聯(lián)冶煉工藝,澆注采用冷調、一體化孔板流量計工藝,在生產過程中前期經常發(fā)生一體化孔板流量計關不住---大漏鋼事故,關不嚴---喇叭口澆注情況,對鑄件澆注質量以及成本構成嚴重影響,由于我公司是鐵路內*一家采用上述工藝,存在裝備、技術狀態(tài)不明確的情況,作業(yè)方式變化所導致技能暫時缺失的困境。通過全面調查影響因數,找出問題點,采取改進措施,解決長期的技術難題。
1 現狀調查
1.1 偏心爐+LF 爐雙聯(lián)冶煉工藝,鋼包冷調、熱裝一體化孔板流量計工藝路線圖簡介如圖 1。
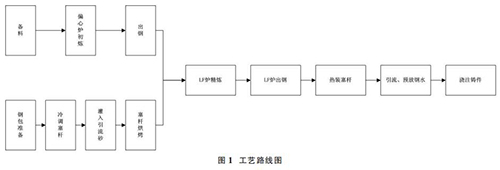
1.2 引流鋼統(tǒng)計如表 1 所示
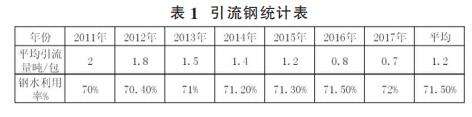
1.3 影響要素分析
1.3.1 我們參照人、機、料、法、環(huán)、測量六要素進行了問題摸排,繪制了問題魚刺圖 2。
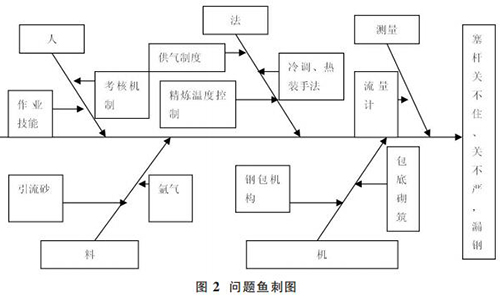
1.3.2 通過末端因素法確定了以下主要因素:
①熱裝后鋼包一體化孔板流量計頭部與水口磚間隙不足,失去下降動能,不利于引流后塞頭完全滑入水口窩內,導致關閉失靈。
②LF 精煉過程導致鋼包上下層鋼水溫度不均勻,尤其是底部偏低---20 噸鋼包內部高度 1.8m,靠鋼液上方三根電*加熱,底部通過透氣磚聯(lián)接氬氣進行全程吹氬精煉。而氬氣是低溫的(液態(tài)轉化為氣態(tài)),所以造成上熱下冷的情況,同樣因偏心爐出鋼加入 400kg 的合金也會造成鋼水劇烈降溫,尤其是底部區(qū)域,而底部鋼水溫度過低,導致鋼水發(fā)粘,影響塞頭閉合,更嚴重會導致塞頭“凍住”打不開。
③引流沙加入量的影響:我們選用的是鉻質引流砂--其主要成分為鉻鐵礦砂,在鑄造中常用作鑄件型腔內部需快速冷卻部位用料。所以當加入量過多會導致鋼包水口處鋼水凍結,如需沖開,需較多的鋼水方行,所以導致引流鋼水量大。
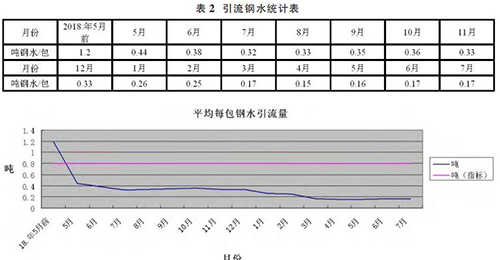
④新砌筑鋼包由于注水口磚高度 290mm,而包底其他部位厚度 350mm,如氬氣口處,造成注水口窩處凹陷過深,此處鋼水氬氣攪拌不到,也會造成該處鋼水溫度過低的情況。
⑤由于存在精煉鋼水溫度不均勻的情況對引流產生巨大影響。
2 改進措施及對策
2.1 鋼包機構改進
通過將鋼包主軸底部加焊 30mm 墊塊將機構主軸上升定位銷孔進行了抬高處理,同時明確了安裝注水口磚尾部時與鋼包底部相對位置要求(凸出底部 2cm 以上)。解決了熱裝后鋼包一體化孔板流量計頭部與水口磚間隙不足的問題。
2.2 鋼水溫度均勻性
通過增加精煉鋼水進站測溫,記錄的工藝要求結合鋼包烘烤情況判斷偏心爐出鋼溫度是否到達技術要求,避免了精煉初期鋼水溫度過低的影響。增添了流量計,通過將精煉吹氬供氣,分三個階段制定了氬氣流量工藝參數,充分利用氬氣攪拌作用使鋼水上下層趨于均勻一致。通過改進了鋼包底部砌筑工藝,解決了水口座磚處相較其他部位過深所導致的局部鋼水溫度過低的問題。從而大大改善了鋼包內鋼水溫度均勻性。
2.3 氬氣供應改進
用杜瓦罐替代了瓶裝氬氣,對氬氣供應方式進行了改進,確保供氣長期穩(wěn)定一致。
2.4 規(guī)范引流砂用量
明確了引流砂加入要求,在注水口窩處堆高20mm 即可,使用量降至原先的 1/3。
2.5 改進作業(yè)規(guī)范、制定應急預案
通過改進一體化孔板流量計冷調作業(yè)規(guī)范和過跨要求以及熱裝時的作業(yè)次序和制定特殊情況下的應急預案,使得一體化孔板流量計跑偏關不嚴的情況得以解決。
2.6 建立考核機制
通過將搭班電爐班與澆注班變?yōu)橐粋€考核單元,對 3 個考核單元(我 3 個電爐+3 個澆注班)建立*獎末罰的聯(lián)動競爭機制,解決了職責不分,獎罰不明的情況,提高了員工積*性。
3 改進后效果
3.1 引流鋼水量大幅下降,降幅達 80%
經過改進后,平均每包鋼水引流量由原先的 1.2 噸降到目前的 0.25 噸,由此節(jié)約電耗:(1.2 噸-0.25 噸)/爐*700kWh/噸 *0.6 元/噸 *2000 爐/年=79.8 萬元。鋼水利用率由 71.5%提升到 75%。同時日生產任務兌現率,由原先的 95%提高到目前的 99%。如表 2、圖 3 所示。
3.2 漏包澆注廢品大幅下降
改進后每月減少了因漏包澆注所導致的澆不足等搖枕側架廢品數量由原先月 25 只降到目前的 4 只,由此年減少廢品損失 25 萬元。車間廢品率由原先的 1%下降到目前的 0.5%。具體情況如圖 4 所示。
3.3 漏包澆注導致的砂箱披縫大幅減少
經過改進后,大幅減少了漏包澆注所導致的砂箱披縫產生,砂箱清理風割人員由原先的 5 人降為 1 人,年節(jié)約人工成本 20 萬元。
4 結論
①通過對鋼包機構的改進,以及鋼包冷調、一體化孔板流量計工藝操作手法的改進確保了一體化孔板流量計與水口磚相互配合的嚴密的要求。
②通過對電爐精煉工藝參數的優(yōu)化等措施確保了整包鋼水溫度的均勻性。
③通過對鋼包底部砌筑工藝的改進,避免了水口磚處凹陷深所造成的局部鋼水溫度過低的危害。
④通過建立聯(lián)動考核機制使得員工作業(yè)質量得到明顯提升。綜上所述,通過有針對性的改進后,引流鋼水量大幅下降 80%,鋼水利用率上升 3%。
引言 我公司自 2009 年技改后,電爐采用偏心爐+LF 爐雙聯(lián)冶煉工藝,澆注采用冷調、一體化孔板流量計工藝,在生產過程中前期經常發(fā)生一體化孔板流量計關不住---大漏鋼事故,關不嚴---喇叭口澆注情況,對鑄件澆注質量以及成本構成嚴重影響,由于我公司是鐵路內*一家采用上述工藝,存在裝備、技術狀態(tài)不明確的情況,作業(yè)方式變化所導致技能暫時缺失的困境。通過全面調查影響因數,找出問題點,采取改進措施,解決長期的技術難題。
1 現狀調查
1.1 偏心爐+LF 爐雙聯(lián)冶煉工藝,鋼包冷調、熱裝一體化孔板流量計工藝路線圖簡介如圖 1。
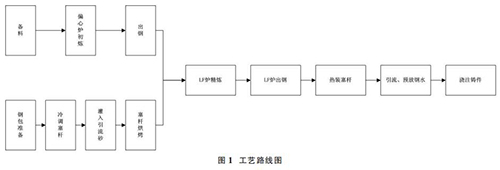
1.2 引流鋼統(tǒng)計如表 1 所示
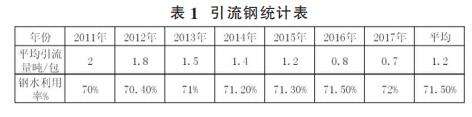
1.3 影響要素分析
1.3.1 我們參照人、機、料、法、環(huán)、測量六要素進行了問題摸排,繪制了問題魚刺圖 2。
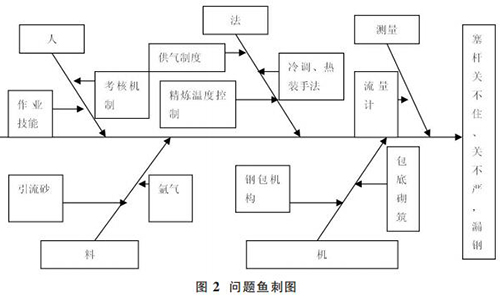
1.3.2 通過末端因素法確定了以下主要因素:
①熱裝后鋼包一體化孔板流量計頭部與水口磚間隙不足,失去下降動能,不利于引流后塞頭完全滑入水口窩內,導致關閉失靈。
②LF 精煉過程導致鋼包上下層鋼水溫度不均勻,尤其是底部偏低---20 噸鋼包內部高度 1.8m,靠鋼液上方三根電*加熱,底部通過透氣磚聯(lián)接氬氣進行全程吹氬精煉。而氬氣是低溫的(液態(tài)轉化為氣態(tài)),所以造成上熱下冷的情況,同樣因偏心爐出鋼加入 400kg 的合金也會造成鋼水劇烈降溫,尤其是底部區(qū)域,而底部鋼水溫度過低,導致鋼水發(fā)粘,影響塞頭閉合,更嚴重會導致塞頭“凍住”打不開。
③引流沙加入量的影響:我們選用的是鉻質引流砂--其主要成分為鉻鐵礦砂,在鑄造中常用作鑄件型腔內部需快速冷卻部位用料。所以當加入量過多會導致鋼包水口處鋼水凍結,如需沖開,需較多的鋼水方行,所以導致引流鋼水量大。
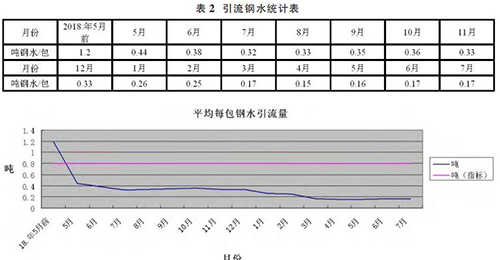
④新砌筑鋼包由于注水口磚高度 290mm,而包底其他部位厚度 350mm,如氬氣口處,造成注水口窩處凹陷過深,此處鋼水氬氣攪拌不到,也會造成該處鋼水溫度過低的情況。
⑤由于存在精煉鋼水溫度不均勻的情況對引流產生巨大影響。
2 改進措施及對策
2.1 鋼包機構改進
通過將鋼包主軸底部加焊 30mm 墊塊將機構主軸上升定位銷孔進行了抬高處理,同時明確了安裝注水口磚尾部時與鋼包底部相對位置要求(凸出底部 2cm 以上)。解決了熱裝后鋼包一體化孔板流量計頭部與水口磚間隙不足的問題。
2.2 鋼水溫度均勻性
通過增加精煉鋼水進站測溫,記錄的工藝要求結合鋼包烘烤情況判斷偏心爐出鋼溫度是否到達技術要求,避免了精煉初期鋼水溫度過低的影響。增添了流量計,通過將精煉吹氬供氣,分三個階段制定了氬氣流量工藝參數,充分利用氬氣攪拌作用使鋼水上下層趨于均勻一致。通過改進了鋼包底部砌筑工藝,解決了水口座磚處相較其他部位過深所導致的局部鋼水溫度過低的問題。從而大大改善了鋼包內鋼水溫度均勻性。
2.3 氬氣供應改進
用杜瓦罐替代了瓶裝氬氣,對氬氣供應方式進行了改進,確保供氣長期穩(wěn)定一致。
2.4 規(guī)范引流砂用量
明確了引流砂加入要求,在注水口窩處堆高20mm 即可,使用量降至原先的 1/3。
2.5 改進作業(yè)規(guī)范、制定應急預案
通過改進一體化孔板流量計冷調作業(yè)規(guī)范和過跨要求以及熱裝時的作業(yè)次序和制定特殊情況下的應急預案,使得一體化孔板流量計跑偏關不嚴的情況得以解決。
2.6 建立考核機制
通過將搭班電爐班與澆注班變?yōu)橐粋€考核單元,對 3 個考核單元(我 3 個電爐+3 個澆注班)建立*獎末罰的聯(lián)動競爭機制,解決了職責不分,獎罰不明的情況,提高了員工積*性。
3 改進后效果
3.1 引流鋼水量大幅下降,降幅達 80%
經過改進后,平均每包鋼水引流量由原先的 1.2 噸降到目前的 0.25 噸,由此節(jié)約電耗:(1.2 噸-0.25 噸)/爐*700kWh/噸 *0.6 元/噸 *2000 爐/年=79.8 萬元。鋼水利用率由 71.5%提升到 75%。同時日生產任務兌現率,由原先的 95%提高到目前的 99%。如表 2、圖 3 所示。
3.2 漏包澆注廢品大幅下降
改進后每月減少了因漏包澆注所導致的澆不足等搖枕側架廢品數量由原先月 25 只降到目前的 4 只,由此年減少廢品損失 25 萬元。車間廢品率由原先的 1%下降到目前的 0.5%。具體情況如圖 4 所示。
3.3 漏包澆注導致的砂箱披縫大幅減少
經過改進后,大幅減少了漏包澆注所導致的砂箱披縫產生,砂箱清理風割人員由原先的 5 人降為 1 人,年節(jié)約人工成本 20 萬元。
4 結論
①通過對鋼包機構的改進,以及鋼包冷調、一體化孔板流量計工藝操作手法的改進確保了一體化孔板流量計與水口磚相互配合的嚴密的要求。
②通過對電爐精煉工藝參數的優(yōu)化等措施確保了整包鋼水溫度的均勻性。
③通過對鋼包底部砌筑工藝的改進,避免了水口磚處凹陷深所造成的局部鋼水溫度過低的危害。
④通過建立聯(lián)動考核機制使得員工作業(yè)質量得到明顯提升。綜上所述,通過有針對性的改進后,引流鋼水量大幅下降 80%,鋼水利用率上升 3%。